ASG AMF based in Bromborough, The Wirral, is a well established subcontract precision engineering company with over 35 years of experience, investing continuously in the latest CNC machining capabilities.
ASG AMF have developed expertise in manufacturing:
Ultra High Vacuum components and assemblies for the Semiconductor Sector
Umbilical components for subsea and other offshore sectors
Cryogenic, mass spectrometry and equipment for Research facilities across Europe equipment
Critical parts for Aerospace, MoD, Oil and Gas and Nuclear sectors
We seek to offer our customers solutions that can meet the needs of the most demanding marketplace. Whether it be a component part or a complex assembly we are committed to producing a high quality product delivered on time, every time.
28,000 sq. ft with additional office space
EPC A-rating
BREEAM Rating: Excellent
Photovoltaic cells on roof
Steel portal construction with Energy efficient cladding system
Capabilities
-
Extensive experience in simultaneous 5 axis machining of Process Chambers up to 800mm cube. We also have the capability in machining long parts up to 3000mm in length x 800mm wide. We primarily work in aluminium and stainless steel, but have experience in various copper alloys; plastics; carbon steel; titanium; and other alloys.
-
We have a range of machines, small bar fed machines for parts up to 65mm diameter (one off to large batch quantities); larger machines capable of machining up to 1000mm diameter x 1000mm long (depending on weight).
-
We have recently invested in an automated Aluminium Arc spraying booth, this process is typically used for corrosion protection and wear resistance. Investing in a robotic arm gives us the advantage of programming for a consist deposit on batch work and also allows us the flexibility of manual spraying small batch work.
We also offer manual Flame spraying which is a thermal spraying process applying metallic coating using heat.
-
We are able to offer TiG, MiG, MMA and brazing, plus orbital welding and vacuum leak detection to 10-12 mbar ls-1. We weld a variety of materials including aluminum, steel and various special alloys in accordance with British and International standards.
We employ automated rotary welding machines (Orbimatic System 160C) to ensure that high precision components are of a high level of repeatability and reliability.
-
Our EDM (Electrical Discharge Machining) machine offers the ability to cut hard materials of a complex nature in a cost effective way, both in semi-automatic and fully non-interactive modes. They are capable of prototyping, developing complex components with very close tolerances and increased efficiency and productivity over traditional techniques.
-
We offer UHV cleaning of parts using a variety of Aqueous solutions. This capability is offered not just for parts manufactured in house, but we offer the same service on a sub contract basis. Typically these parts are used in an Ultra High Vacuum application.
-
Our clean assembly facility meets the highest standards of dust free environment and our customers’ assembly expectations. We are able to build electro-mechanical assemblies free of contamination in a controlled temperature room satisfying the needs of high specification industries such as semiconductor, medical and pharmaceutical, life sciences and aerospace.
-
ASG Group has invested in a new thermal spray capability, situated at AMF Precision Engineering Ltd in Bromborough. The thermal spray equipment, used in conjunction with a state-of-the-art six-axis KUKA robot, will help us meet growing demand for high-quality thermal spray coatings for aerospace components within our world class customer base.
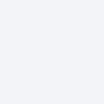
Frequently Asked Questions
-
3-axis machine centres, also known as 3-axis machining centres or milling machines, are precision machining tools used in manufacturing and prototyping processes. The term "3-axis" refers to the three-dimensional movement capabilities of the machine along three mutually perpendicular axes: X, Y, and Z. Here's a brief overview of each axis:
X-axis: Horizontal movement from left to right or vice versa. The X-axis represents the longitudinal movement of the machine.
Y-axis: Horizontal movement from front to back or vice versa. The Y-axis represents the lateral movement of the machine.
Z-axis: Vertical movement up and down. The Z-axis represents the vertical movement of the machine.
These three axes allow for precise control over the position and depth of the cutting tool, enabling the machine to create complex and intricate shapes on a workpiece. 3-axis machining centres are commonly used in various industries, including aerospace, automotive, electronics, and general machining, for tasks such as milling, drilling, and engraving.
It's worth noting that there are also machines with more axes, such as 4-axis and 5-axis machining centers, which offer additional rotational movements around specific axes. These extra axes provide increased flexibility for machining more complex geometries and reducing the need for multiple setups.
-
3-axis CNC machining offers several advantages, making it a versatile and widely used technology in various manufacturing industries. Here are some key advantages:
Simplicity and Cost-Effectiveness
Ease of Programming: The programming of 3-axis CNC machines is generally simpler compared to machines with more axes. Many operators and programmers are familiar with 3-axis systems, making it easier to find skilled personnel.Lower Costs: 3-axis CNC machines are often more affordable than machines with additional axes, both in terms of initial investment and ongoing maintenance.
Versatility
Wide Range of Applications: 3-axis CNC machines are suitable for a broad range of applications, including milling, drilling, and engraving. They can handle a variety of materials, making them versatile for different industries.Ease of Use
User-Friendly: The operation of 3-axis CNC machines is relatively straightforward, making them accessible to operators with varying levels of experience. This ease of use contributes to increased productivity.High Precision
Accurate Machining: 3-axis machines are capable of high-precision machining, ensuring tight tolerances and excellent repeatability. This precision is crucial for industries that require accurate and consistent parts.Reduced Set-Up Time
Simplified Set-Up: Setting up a 3-axis CNC machine is generally quicker and simpler than setting up machines with more axes. This can lead to shorter lead times for production runs.Widespread Availability of Tooling
Standard Tooling: Standard tooling and accessories are widely available for 3-axis machines, contributing to cost-effectiveness and ease of tool replacement.Proven Technology
Reliability: 3-axis CNC machining is a well-established and reliable technology. Manufacturers have been using these machines for decades, and they have a proven track record of delivering consistent results.While 3-axis CNC machining has these advantages, it's important to note that for more complex geometries and intricate designs, higher-axis machines (such as 4-axis and 5-axis) may be necessary to achieve certain machining tasks efficiently. The choice between different axis configurations depends on the specific requirements of the project.
-
Lights out machining refers to a manufacturing process in which CNC (Computer Numerical Control) machines operate without the need for direct human intervention. The term "lights out" is derived from the idea that the facility can essentially turn off the lights and continue production without human presence. This concept relies on automation and advanced technologies to enable continuous and unmanned machining operations.
Key characteristics of lights out machining include
Automation: Lights out machining heavily relies on automated systems, including CNC machines, robotic loaders, tool changers, and other peripherals. These systems work together seamlessly to perform various manufacturing tasks without the need for constant human oversight.Unmanned Operation: Once the machining process is set up and initiated, human operators are not required to be present for the duration of the production run. This can lead to increased efficiency, reduced labour costs, and the ability to run production continuously, including overnight and during weekends.
Advanced Monitoring and Control Systems: Lights out machining often involves sophisticated monitoring and control systems. These systems can include sensors, cameras, and software that allow operators to remotely monitor the status of the machines, detect issues, and make adjustments as needed.
Optimised Workflow: Lights out machining is particularly suitable for repetitive and high-volume production runs where the workflow can be optimised for efficiency. It helps minimise downtime between batches and ensures a more continuous production cycle.
Reduced Lead Times: By allowing machines to run continuously, lights out machining can contribute to reduced lead times for production orders. This is especially beneficial for industries with demanding production schedules.
Cost Savings: Lights out machining can result in cost savings by minimizing labour costs, maximizing machine utilisation, and reducing the need for manual intervention. It can lead to improved productivity and competitiveness in the manufacturing sector.
While lights out machining offers significant advantages in terms of efficiency and cost savings, it also presents challenges. Advanced planning, robust automation systems, and reliable monitoring are essential to ensure the successful implementation of lights out operations. Additionally, the suitability of lights out machining depends on the specific requirements of the manufacturing process and the complexity of the parts being produced.
-
5-axis CNC machining is a sophisticated manufacturing process that involves the use of a computer numerical control (CNC) machine with five axes of motion. Unlike 3-axis machining, which operates along the X, Y, and Z axes, 5-axis machining adds two more rotational axes—usually referred to as A and B or sometimes called the rotary axes. These additional axes allow the cutting tool to move in multiple directions, providing greater flexibility and the ability to produce more complex and intricate geometries.
The five axes in a 5-axis CNC machine are typically defined as follows:
X-axis: Horizontal movement from left to right or vice versa.
Y-axis: Horizontal movement from front to back or vice versa.
Z-axis: Vertical movement up and down.
A-axis: Rotation around the X-axis, allowing the cutting tool to tilt.
B-axis: Rotation around the Y-axis, enabling the cutting tool to swivel.
The combination of linear and rotational movements allows the cutting tool to approach the workpiece from multiple angles, making it possible to machine complex surfaces and contours in a single setup. This capability is especially valuable in industries such as aerospace, automotive, and medical, where parts with intricate shapes and tight tolerances are common.
-
Key advantages of 5-axis CNC machining include
Increased Precision: The ability to approach the workpiece from various angles enhances precision and accuracy, especially when machining complex contours.Reduced Set-Up Time: With 5-axis machining, multiple sides of a part can be machined in a single setup, reducing the need for repositioning and fixture changes.
Versatility: 5-axis machines are versatile and can handle a wide range of part geometries without the need for multiple setups.
Enhanced Surface Finish: The multi-axis movement allows for better tool engagement, resulting in improved surface finishes on the machined parts.
Efficiency in Production: 5-axis machining can increase efficiency by reducing the number of setups required for complex parts, ultimately reducing production time.
While 5-axis CNC machining offers numerous advantages, it also requires a higher level of programming and expertise. The complexity of the machines and the need for precise toolpath planning make it essential for operators and programmers to have a deep understanding of the technology.
-
CMM capability refers to the performance and accuracy of a Coordinate Measuring Machine (CMM) in measuring and inspecting geometric features of manufactured parts. A CMM is a specialised device used in manufacturing and quality control processes to measure the dimensions, angles, and shapes of objects with high precision. The capability of a CMM is influenced by various factors, and understanding these capabilities is crucial for ensuring accurate and reliable measurements. Here are some key aspects of CMM capability:
Accuracy: Accuracy is a measure of how closely the measured values obtained by the CMM match the true or nominal values of the measured features. CMM accuracy is affected by factors such as the machine's design, calibration, environmental conditions, and the quality of its components.
Repeatability: Repeatability refers to the ability of the CMM to produce consistent measurements when measuring the same part repeatedly. A CMM with high repeatability will provide similar results each time it measures the same part under the same conditions.
Resolution: Resolution is the smallest incremental movement that a CMM can detect. Higher resolution allows the CMM to measure finer details and features. It is an important factor when measuring small or intricate components.
Probing System: The probing system of a CMM includes the type of probe used and its capabilities. Different probes are designed for specific measurement tasks, such as touch-trigger probes for discrete point measurements or scanning probes for continuous surface measurement.
Software Capabilities: The software used to control and analyse data from the CMM plays a crucial role in its capability. Modern CMM software allows for advanced measurement strategies, geometric dimensioning and tolerancing (GD&T) analysis, and statistical process control.
Environmental Conditions: The operating environment, including temperature, humidity, and cleanliness, can affect CMM performance. Some CMMs are equipped with environmental monitoring systems to compensate for changes in conditions.
Machine Stability: The stability of the CMM structure and its components is critical for maintaining accuracy. Factors such as thermal stability and rigidity of the machine contribute to its overall capability.
Calibration and Maintenance: Regular calibration and maintenance are essential for ensuring that a CMM continues to operate within specified tolerances. Calibration helps verify the accuracy of measurements and correct any deviations.
CMM capability is typically expressed in terms of its uncertainty or the range within which measurements are expected to be accurate. Understanding the capability of a CMM is crucial for establishing confidence in the metrology processes and ensuring that manufactured parts meet specified quality standards. Manufacturers often perform capability studies to assess and document the performance of their CMMs in real-world applications.
-
Benefits
Residual Stress: Shot peening induces compressive residual stresses in the treated material, improving its resistance to fatigue and preventing the initiation and propagation of cracks.Improved Strength: The process can enhance the strength and load-bearing capacity of components.
Surface Hardening: Shot peening can also contribute to surface hardening, increasing wear resistance.
Applications
Aerospace: Shot peening is commonly used in the aerospace industry to enhance the fatigue life of critical components such as turbine blades, landing gear, and engine parts.Automotive: Automotive applications include the treatment of various engine and transmission components to improve durability.
General Manufacturing: Shot peening is applied to a wide range of metal components in general manufacturing to improve their performance under cyclic loading.
Shot peening is a controlled process that requires careful consideration of parameters such as shot size, intensity, and coverage to achieve the desired results. It is an effective method for extending the life and reliability of metal parts subjected to fatigue and stress in various industrial applications.
-
CNC turning and CNC milling are two distinct machining processes, each suited for specific types of workpieces and applications. Here are the key differences between CNC turning and CNC milling:
Process Orientation
CNC Turning: Turning is a process that involves rotating a workpiece while a cutting tool is traversed along it to remove material and create cylindrical shapes. The workpiece is held in a chuck and rotates on its axis. This process is ideal for creating cylindrical or conical shapes, such as shafts, pins, and bushings.CNC Milling: Milling is a process that involves removing material from a workpiece using rotating cutting tools. The workpiece remains stationary, while the milling machine's spindle and cutting tools move in multiple directions to shape the material. Milling is suitable for creating a wide range of shapes, including flat surfaces, slots, and complex three-dimensional contours.
Tool Movement
CNC Turning: In turning, the cutting tool moves parallel to the axis of rotation of the workpiece. The tool is fed along the length of the rotating workpiece to remove material and shape it.CNC Milling: In milling, the cutting tool can move along the X, Y, and Z axes. This multi-directional movement allows for the creation of intricate shapes and features on the workpiece.
Workpiece Shapes
CNC Turning: Turning is well-suited for producing cylindrical or rotationally symmetric parts. It is commonly used for creating components like shafts, bolts, and bushings.CNC Milling: Milling is versatile and can be used to create a wide range of shapes, including complex contours, pockets, slots, and intricate three-dimensional geometries.
Typical Applications
CNC Turning: Turning is often used for parts with rotational symmetry, such as components in the automotive industry (e.g., crankshafts) and in the production of round or tubular components.CNC Milling: Milling is employed for a broad range of applications, including the production of flat and contoured surfaces in aerospace, mould making, and general machining.
Machine Configuration
CNC Turning: Turning machines, also known as lathes, are configured to hold and rotate the workpiece while the cutting tool moves along the length of the part.CNC Milling: Milling machines are equipped with a stationary worktable, and the cutting tool moves in different directions to shape the workpiece. CNC milling machines may be vertical or horizontal, depending on the orientation of the spindle.
In summary, CNC turning is best suited for producing cylindrical or rotationally symmetric parts, while CNC milling is more versatile and suitable for creating a wide range of shapes, including complex three-dimensional geometries. The choice between turning and milling depends on the specific requirements of the part and the desired features of the final product.
Contact Us
ASG AMF Precision Engineering Limited, Unit 3 & 5, The Power Station Business Park, Thermal Road, Bromborough, Wirral, CH62 4YB
Phone
+44 (0)151 346 1166
Policies
-
1. General
The acceptance of this tender includes the acceptance of the following terms and conditions and no alteration, variation, departure therefrom or addition thereto, oral or written, shall affect or be binding upon us, unless our consent in writing shall have been given. Any special conditions, where applicable, will over-ride general conditions inconsistent with the special conditions.
2. Period of Tender
This tender is conditional upon acceptance in writing within thirty days of the date hereof or such longer periods as may be agreed in writing.
3. Delivery
When the price quoted includes delivery, we will repair or replace free of charge goods damaged in transit provided written notification of such damage is sent to and received by ourselves and the Carriers within three days of delivery but not otherwise.
The delivery periods stated are from receipt of official instructions from the Customer /Purchaser to proceed.
4. Delay
If, for any reasons beyond our control, we are not able to carry out the installation in accordance with the programme referred to in the tender, or such other programme as may be accepted by us, our time for completion shall be extended and we shall be paid, as an addition to the tender price, such extra costs (all such costs of whatever nature) as may be attributable to such delay. This applies to both fixed and fluctuating price tenders.
Where time for delivery and/ or completion is specified, every reasonable endeavour will be made to adhere thereto, but no liability for any loss whatsoever shall attach to us for delay, which is beyond our control in delivery or completion.
5. Installation of Services, Plant and Equipment
5.1. Where erection is included by us, we will provide a suitable number of Erectors necessary in our absolute opinion to carry out the work in normal hours. We do not include for any overtime or Saturday or Sunday work. If, therefore, we are required to work any additional time over normal hours per week, this will be chargeable as an extra to contract at the appropriate time rate.
5.2. This tender is exclusive of any extra work that may be entailed in taking down and refixing for the convenience of other Trades after
Installation has once been carried out.
5.3. Unless otherwise expressly stated, this tender does not include:
a) foundations and supports;
b) Builders and all other trades work except as allowed in the specification;
c) supply and erection of scaffolding, ladders or movable platforms; hoisting and/or lowering gear; (iv) the cost of fuel and water for testing and other purposes, electric current for motors and lighting; (v) fees of District Surveyors, Architects,Quantity Surveyors,Structural Engineers , Insurance Inspectors or any other inspecting authority
5.4. We shall not be responsible for any damage to or loss of tools and equipment, including free issue items, made available to us by the Customer/Purchaser
5.5. We shall not be liable for any loss or damage direct or indirect nor for any extra work entailed, due to the apparatus being put into operation by the Customer/Purchaser (or by us at his request) before the contract is completed and the apparatus is commissioned for use. Should we be requested to put the installation into service before completion of the contract, our guarantees and defects liability periods commence from the date that the installation is put into service.
5.6. We do not include costs for work which may be necessary due to expenditure for work represented by the provisional sums (P.S.) in this tender. This expenditure will only be ascertained upon completion of the work, and such expenditure will replace the figure stated as provisional sums and shall be payable by the Customer/Purchaser. Unless specifically stated , we do not include within our programme the time necessary to carry out the work against provisional sums.
5.7. Two copies where appropriate, of the Main Contractors programme , incorporating our agreed programme, shall be forwarded to us within two weeks of receipt by the Customer/Purchaser.
5.8. The passing of risk shall not be delayed on account of additions, minor omissions or defects which do not materially affect the operation of the plant.
5.9. In the case of scales equipment, customers will pay for stamping fees and for expenses incurred for transport etc. of inspectors test weights and/ or equipment. Customers will allow free use of their test weights or pay for expenses incurred in transporting our test weights.
6. Terms of Payment
6.1. Payment (excluding that relevant to scales equipment and service and that relevant to deposits for plant items) during the progress of the work shall be made monthly, at the rate of 95% of the value of materials delivered on the site (whether fixed or unfixed) and of the value of the work executed, such payment to be made within fourteen days of the application, time to be of the essence, and if such payment is not made , then we may suspend or abandon the work and remove unfixed materials, tools and other equipment from the site. Where deposits or stage payments are payable by us in connection with plant items, this will be payable by customers in advance of delivery to site as liability is incurred, non-returnable payment to be made within fourteen days of application.
6.2. The balance to be paid four weeks after completion (without being liable for any loss of whatever nature), time to be of the essence.
6.3. Where cash discount is included, this will be allowed only if payment is received by us within fourteen days of application.
6.4. In no case shall any dispute concerning any other contract affect the Customer/Purchaser’s obligations in respect of this contract.
6.5. In the case of scales equipment and service, payment is due on completion of contract or delivery of goods.
6.6. In no case shall any dispute concerning any part or portion of the goods or work affect the Customer/ Purchaser’s obligation in respect of other parts or portions.
6.7. This contract is divisible. Each delivery made hereunder:
a) shall be deemed to arise from a separate contract, and
b) shall be invoiced separately and any invoice for a delivery shall be payable in full in accordance with the terms of payment provided herein without reference to and not withstanding any defect or default in the delivery of any other instalments.
7. Price Fluctuations
7.1. Unless expressly stated to be on a firm price basis, this tender is based on the market prices and rates of materials, labour, sub-contracts and transport ruling fourteen days before the date of tender. We reserve the right to amend the tender price and rates to cover the variations in these prices and rates owing to Legislation, Government Orders, Regulations or Directions, changes in the National Agreements covering wages and conditions in the industry or any cause beyond our control occurring between the dates of the tender and the completion of the work.
Unless otherwise stated, fluctuations will be calculated in accordance with the National Economic Development Office (N.E.D.O. – N.C.C.) Formulae for Specialist Engineering Installations.
7.2. Where no price has been fixed or agreed at the time of our acceptance of the order , the price shall be that current at the time of delivery or completion of the work.
7.3. In those instances where we have tendered on a firm price basis, should the work proceed after the expiry of the firm price period, fluctuations will be calculated as if normal fluctuations were applicable from commencement of the contract less the fixed price element for anticipated cost increases included in our tender. This balance will become due to us within fourteen days of our invoice.
8. Variations
The Customer/Purchaser or his duly appointed agent may authorise the carrying out of extra work and of variations to the installation, but we shall not be obliged to do any extra work or to make any variations until:
8.1. The same shall first have been authorised in writing by the Customer/Purchaser or his agent, and agreed by us, and
8.2. The value thereof has been agreed where it is reasonably possible to estimate the same.
If it shall not be possible to estimate the value thereof before the extra or varied work is carried out, or if the extra or varied work shall be commenced before the valuation thereof has been agreed, a fair valuation shall be made after it has been carried out.
Should any variation have the effect of reducing the contract sum, we reserve the right to make provision for the loss of establishment and sight overheads which would otherwise have been recovered had the variation not taken place.
Where a price has been agreed for acceleration of the works, the agreed sum will be due to us whether or not the works are completed by the revised agreed date for completion owing to any matter for which we are not responsible.
Where variations materially affect our agreed contract period, that period will be extended by whatever time is necessary to complete the variations carried out, and we shall be entitled to payments for loss and expense incurred owing to the extended contract period.
9. Guarantee
9.1. W guarantee all machinery and materials of our manufacture against defects in workmanship and material for one year from the time of delivery and will, at our option, repair or replace such products as we find defective.
9.2. On machinery and materials furnished by us but manufactured by others, we will extend the same guarantee received from the Manufacturers and where such guarantee and rights thereunder are assignable.
9.3. Any liability in contract or at common law of whatever nature, and loss arriving thereof in respect of any machinery, workmanship or materials, whether manufactured by us or otherwise, shall not in any case exceed the cost of correcting such defects.
9.4. The warranties and guarantees herein set forth are made by us and accepted by the Customer/Purchaser in lieu of all statutory or implied warranties or guarantees, other than the title and where such statutory or implied warranties or guarantees are possible to exclude by agreement.
9.5. We reserve the right to change the construction or design of the machinery and materials. If in our absolute discretion, such change is to the interest of all parties, so long as their general function is not thereby altered.
9.6. The Contractor shall not be liable for any loss of profit or produce or any consequential loss or damage resulting from the breach of any provision of this contract, including any express or implied warranty or guarantee, except in so far as this exclusion is rendered void by law.
9.7. This contract contains all agreements between the parties, and there is no agreement, verbal or otherwise which is not set down herein. No person shall have any right to waive or change any provisions of this contract or to waive any legal rights of ours without written authority from one of the duly authorised representatives.
10. Drawings
Unless expressly stated, drawings submitted by us shall be regarded as general arrangement drawings only, and shall not be binding as to detail. We reserve copyrights to all drawings submitted by us. Three copies only of the appropriate drawings are included for in our tender.
11. Property in Materials and Responsibility for Damage
11.1. Until we have been paid in full for the goods comprised in this contract by us to the Customer/Purchaser:
a) The goods comprised in this contract remain our property, but all risks shall pass to the Customer/Purchaser on delivery and/or installation in accordance with Clause 5 hereof.
b) If the Customer/ Purchaser incorporates goods supplied or made by us into other products, then those shall be our property; if our goods or products are mixed with other
goods or products the property of which is retained by any other person, then the products or goods shall be out property and such other person in proportion to the cost price of our goods and the other goods.
c) If the Customer/Purchaser disposes of our goods or such products the Customer/Purchaser shall hold and pursue claims for the proceeds of sale on trust on our behalf.
11.2. All materials on the site, fixed or unfixed, are to the sole risk of the Customer/Purchaser and in the event of any of the same being damaged, destroyed or stolen, we shall be entitled to full payment therefore, and also for any work damaged, destroyed or lost, and the cost of replacing any such materials and of reinstating or restoring any such work, shall be charged as an extra.
11.3. TheCustomer/ Purchaser shall be solely responsible for all loss or damage to the work or to any plant, tools, equipment and unfixed materials properly on the site for the purpose of carrying out the work arising from fire, storm, tempest, lightning, flood, explosion and bursting or overflowing of water tanks , apparatus or pipes, earthquake, aircraft or anything dropped therefrom, aerial objects, riot and civil commotion or any other cause, even if such peril was caused or contributed to by negligence of ourselves or of our sub-contractors.
11.4. Irrespective of any insurance taken out by us, the Customer/Purchaser should advise his insurers that building/engineering works are being carried out on his property and satisfy himself that he is adequately covered by insurance against loss or damage by fire or other risks arising out of and during the progress of such works. Unless otherwise expressly agreed, we are not liable for loss or damage by fire to the works, materials on site, or any property of the Customer/Purchaser.
12. General Liabilities
We shall not be liable for any claim (other than for negligence resulting in death or personal injury) whether brought against the Customer/Purchaser under the Workmen’s Compensation Acts. Employers Liability Acts, Health and Safety at work Acts, or other Acts of Parliament of a like nature in force for the time being or under statute or at common law arising from any cause or acts of omission upon the part of ourselves, our employees, agents or sub-contractors, and the Customer/Purchaser shall indemnify us against any such claim, except in so far as such indemnity is unreasonable in accordance with statute.
13. Insolvency, etc Customer, Purchaser
If the Customer/Purchaser becomes insolvent or being a body corporate, has passed a resolution for its winding up to be made, or has had a Receiver appointed, or being an individual or partnership has or have suspended payment of his or her debts in whole or in part, or has or have entered into any composition or arrangement with his or their creditors, or has or have had a Receiving Order made against them, then we shall be entitled forthwith, or so long as any of the aforesaid circumstances continue to exist, to terminate the contract in writing to the Customer/Purchaser or any person in whom their interest under the contract has become vested.
14. Value Added Tax
All prices appearing on quotations will be tax exclusive prices. VAT where applicable, will be charged on sales invoices.
Revised June 2022